Accessoires
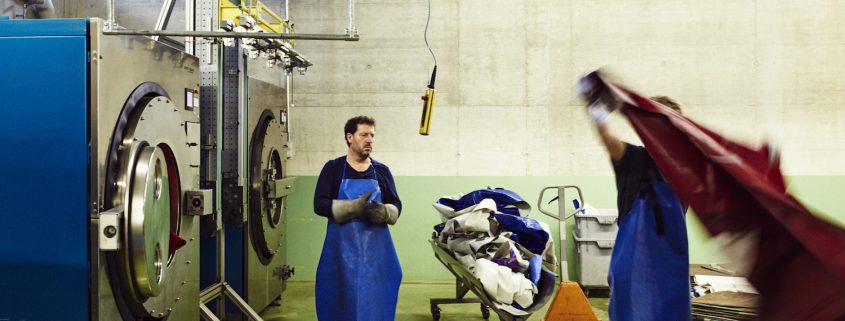
Thank God gibt’s Freitag – 1 Produktionstag bei der Schweizer Taschenmanufaktur
Aus einer Schnapsidee am WG-Wohnzimmertisch entwickelte sich in 25 Jahren ein trendiger Taschenproduzent, der aus 460 Tonnen LKW-Planen jährlich 450.000 unikate Taschen herstellt. Wir durften einen Tag lang mitproduzieren und dem Schweizer Unternehmen FREITAG bei der stetigen Suche nach Nachhaltigkeit behilflich sein.
Text: Jakob Stantejsky
Im Norden der Stadt Zürich liegt das Quartier Oerlikon, wo wiederum ein Gebäude namens NŒRD steht. Dass FREITAG gemeinsam mit einigen anderen Firmen hier im Jahre 2011 sein Hauptquartier aufgeschlagen hat, ist alles andere als ein Zufall. Denn nach knapp zwei Jahrzehnten im Zürcher Kreis 5 hatte sich die Gegend dort derart unvorteilhaft verändert, dass die Gebrüder Freitag gezwungen waren, ein neues Planenhauptquartier aufzuschlagen. Nach langer Suche war dann ein leeres Grundstück gefunden, doch dort für einen Millionenbetrag eine FREITAG-Fabrik aus dem Boden zu stampfen, passte so gar nicht zur nachhaltigen Firmenphilosophie des Schweizer Brüderpaares. Schließlich sammelte man eine Truppe aus Bauunternehmern, Lieferanten, Investoren und Partnern und machte sich an den Bau eines in ökologischer Hinsicht hochmodernen, aber völlig luxusbefreiten Gebäudes, das nunmehr ein Zuhause für eine Handvoll Unternehmen bietet. 7.500 Quadratmeter mietet FREITAG selbst und fertigt hier nicht nur seine Taschen, sondern zelebriert auch die Kunst des Upcyclings mit einer Hingabe, die ihresgleichen sucht.
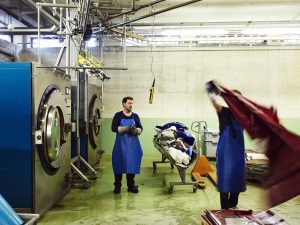
Die frisch zerlegten Planen werden von unserem Redakteur aufgeschüttelt und dann in die Waschmaschine gestopft. Der Experte von FREITAG hat uns kritisch im Blick. Foto: (c) Flavio Leone
Direkt nach unserer Ankunft steigen wir hinab in den unterirdischen Regenwasserbehälter, wo der Niederschlag, der auf dem Dach von NŒRD aufgefangen wird, gesammelt und in weiterer Folge für die Produktion im Betrieb verwendet wird. 350.000 Liter können hier maximal gespeichert werden und vermindern so den Verbrauch an wertvollem Wasser. Das Regenwasser dient zur ersten Wäsche der angelieferten, oft völlig verdreckten Planen. Des Weiteren wird das letzte Spülwasser wiederum zur Erstwäsche der nächsten Plane verwendet. Die Temperatur des verwendeten Wassers wird benutzt, um das gesammelte Regenwasser zu erwärmen. FREITAG recycelt also schon innerhalb der eigenen Fabrik eine ganze Menge. Wobei Fabrik ein Wort ist, das nicht so recht zum FREITAG-Sitz passen will. Denn rauchende Schlote und vollautomatische Roboter sucht man hier vergebens. Es handelt sich eher um einen Handwerksbetrieb mit mehreren Stationen und vielen unterschiedlichen Aufgaben. Aber alles der Reihe nach.
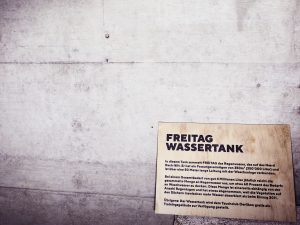
Umweltbewusst: Der FREITAG Wassertank. Foto: (c) Flavio Leone
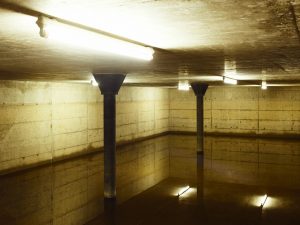
Im Regenwassertank sammelt FREITAG bis zu 350.000 Liter. Foto: (c) Flavio Leone
Nach unserer Tour zum Wassertank begeben wir uns erst einmal dorthin, wo die gebrauchten, dreckigen LKW-Planen angeliefert werden. 460 Tonnen kauft das Unternehmen jährlich in ganz Europa ein. In einer riesigen Halle stehen hier zwei vierzehn Meter lange Tische, auf denen zu diesem Zeitpunkt vier bis fünf Arbeiter damit beschäftigt sind, die riesigen Planen auszubreiten. Flugs bekommen wir einen Cutter und eine Zange in die Hand gedrückt – jetzt heißt es mitarbeiten. Die Ränder der Ungetüme werden abgeschnitten, da sie mit zahlreichen Ösen, Schnallen und Säumen versehen sind, die man in der Taschenproduktion leider nicht gebrauchen kann. Dann geht es daran, die Gurte, die sich kreuz und quer über die Planen ziehen, mit der Zange, ein wenig Technik und vor allem viel roher Gewalt abzureißen. Außerdem werden sämtliche Metallteile nun so entfernt, dass möglichst wenig Material verloren geht. All diese Überbleibsel werden in getrennte Behälter entsorgt und später allesamt in der einen oder anderen Form recycelt oder fachgerecht entsorgt. Nun wird jede Plane in „handliche“ Stücke zerlegt, die immer noch die Größe eines Super-King-Size-Bettlakens haben.
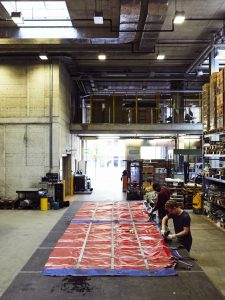
Gemeinsam mit Mustapha zerlegen wir eine komplette LKW-Plane. Das entfernen der Schnallen und Gurte geht ganz schön in die Arme. Foto: (c) Flavio Leone
Zu zweit sind wir mit einem Exemplar erstaunlich rasch fertig, doch spürt man schon nach ein, zwei Durchgängen, wie sich die Muskeln protestierend zu Wort melden. Und es ist fast schon deprimierend, wenn man einen Blick zum anderen Tisch wirft, wo zwei der Vollprofis zugange sind und die Plane mit einem Affenzahn zerstückeln, von dem wir nicht einmal träumen können. Dank der Anleitung von Thomas schlagen wir uns jedoch recht wacker und stapeln die fertigen Teile bald auf, um sie dem nächsten Schritt zuzuführen.
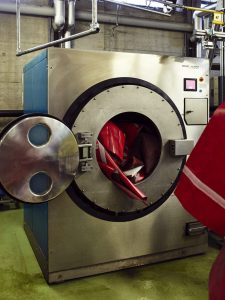
Das Regenwasser kommt in den Waschmaschinen zum Einsatz. Foto: (c) Flavio Leone
Also ab in den Keller, wo die Waschküche wartet. Hier stehen drei riesige Waschmaschinen und eine höchst komplexe, fast schon verwirrende Maschinerie hängt von der Decke herab. Erst einmal ist jedoch alles ganz simpel. Die gefalteten Planenstücke werden aufgeschüttelt und in die Trommeln gestopft. Leichtgewichte sind die Teile keineswegs, aber nach einer Weile sind wir mit der ersten Fuhre fertig. Ungefähr eine Dreiviertelstunde lang arbeitet die Waschmaschine, bevor wir die Planen wieder ausräumen und auf die schon erwähnte, per Knopf bedienbare Trockenvorrichtung hängen. Die zuckelt dann quer durch den Raum bis in das Trockenzimmer, wo mittels warmer Luft die Feuchtigkeit vertrieben wird. In der Folge wird mit einer hochmodernen kleinen Kamera die exakte Farbe, Dicke und das Design des jeweiligen Exemplars charakterisiert und jede Plane bekommt eine Bestimmung verliehen. Anders gesagt: Es wird festgelegt, zu welchem Taschenmodell sie verarbeitet werden soll.
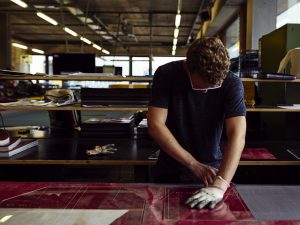
Nach ein paar geführten Versuchen schneidet WIENER-Redakteur Stantejsky selbst einen Rucksack zu. Foto: (c) Flavio Leone
Nun wandern die Planen und wir wieder ein Stockwerk nach oben, wo uns Bag-Designer Mona demonstriert, wie der Zuschnitt für die Taschen erfolgt. Es gibt zwar auch eine Maschine, die das erledigen kann, allerdings braucht auch sie menschliche Hilfe und ein guter Teil der Planen wird schlicht von Hand zerlegt. Dafür gibt es diverse Schablonen, je nach Modell. Nachdem Mona uns zeigt, wie es gemacht wird, dürfen wir selbst einen Versuch wagen. Dabei muss darauf geachtet werden, dass möglichst wenig von der Plane zu Ausschussware wird, allerdings soll das Design ja auch cool werden und dementsprechend müssen wir die Schnittmuster so positionieren, dass sie auf dem fertigen Produkt ein ansehnliches Design ergeben. Hier ist Technik alles, denn wofür Mona ein paar Sekunden und scheinbar überhaupt keine Kraft benötigt, dafür brauchen wir höchste Konzentration und ein gesundes Maß an Nachdruck. Für Letzteres rügt er uns auch immer wieder, denn mit unserer Methode würde man niemals einen achtstündigen Arbeitstag durchhalten – glauben wir ihm sofort. Mit den Überbleibseln, die zwangsläufig doch entstehen, beschäftigen sich weiter hinten ein paar findige Köpfe und schaffen es tatsächlich, fast überall doch noch ein Geldbörserl, eine Handyhülle oder ein Federpennal herauszuquetschen. Bei FREITAG sind sie auf Verschwendung wirklich allergisch.
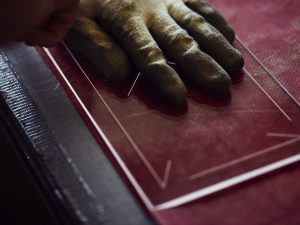
Beim Zuschneiden der Planen ist räumliches Vorstellungsvermögen gefragt. Foto: (c) Flavio Leone
Der einzige Schritt, der nicht hier im NŒRD erledigt wird, ist das Zusammennähen der einzelnen Taschen. Hierfür verschickt FREITAG die penibel sortierten Einzelteile an Nähereien in der Schweiz, Bulgarien, Portugal, Tschechien und Tunesien, von wo dann die fertigen Produkte zurückkommen. Aber FREITAG wäre nicht FREITAG, wenn man die Taschen nicht noch einmal auf Herz und Nieren durchchecken würde. In der Qualitätskontrolle wird jedes einzelne Exemplar individuell in einer dutzende Schritte umfassenden Prozedur von einem Mitarbeiter überprüft. Planenqualität, Nähte, Abstände, nichts entgeht den strengen Augen der Kontrolleure. Schon kleinste Makel werden nach Möglichkeit repariert – oder die betroffenen Produkte werden als „Raritäten“ zum halben Preis im Fabrik-Shop verkauft.
Nun trennen sich die Wege der Teile. Manche zieht es in die Verkaufsräume auf der ganzen Welt, wobei die Verteilung der Unikate – ja, aufgrund der Beschaffenheit der Planen ist wirklich jedes einzelne Produkt ein eigenständiges Einzelstück – gänzlich zufällig vonstatten geht. Die Regale, die zur Aufbewahrung und Präsentation in den Shops verwendet werden, hat FREITAG natürlich auch selbst entwickelt und dabei auf Effizienz und Ressourcenschonung Wert gelegt. Rund 5.000 Exemplare warten außerdem im Onlineshop, dessen Lager sich auch hier im NŒRD befindet, auf ihren Käufer. Jede Tasche wird aus allen Winkeln in einem professionellen Fotostudio abgelichtet, damit der Kunde sich ein umfassendes Bild von seiner Anschaffung machen kann. Knapp zwei Monate dauert es übrigens von der Zerstückelung einer Plane bis hin zum fixfertigen Produkt. Jedes einzelne FREITAG-Teil wird ganz oldschoolig an und mit der Nähmaschine im Musterschneiderei-Atelier im 1. Stock entworfen, wie es Markus und Daniel Freitag vor 25 Jahren schon gemacht haben. Damit bleibt nicht nur die Bodenständigkeit erhalten, es wird auch garantiert, dass jede Näherei die Modelle herstellen kann. Das Modell, das wir durch den Fertigungsprozess begleitet haben, nennt sich übrigens F155 Clapton und zählt nach seinem Launch im März 2018 zu den jüngeren Modellen im Sortiment. Der Rucksack ist nicht nur FREITAG-typisch robust, sondern besitzt auch reflektierende Konturmarkierungen, die im Verkehr für mehr Sicherheit sorgen, egal ob man zu Fuß, im Laufschritt oder auf dem Rad unterwegs ist.
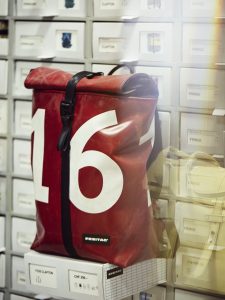
So steht der fertige F155 Clapton dann im Shop, in dem eigens entwickelten FREITAG-Regal. Foto: (c) Flavio Leone
Nach unserem Tag als „Mitarbeiter“ in der FREITAG-Zentrale sind wir schlicht fasziniert. Denn einerseits sind die Abläufe an und für sich simpel und unkompliziert, aber andererseits ergeben sie in ihrer Summe ein Unternehmen, das in seinem ständigen Streben nach Innovation, Umweltbewusstsein und Nachhaltigkeit seinesgleichen sucht. Entstanden ist all das aus dem Nichts. Nicht umsonst waren die LKW-Besitzer früher noch froh über die kostenlose Entsorgung und haben den Freitag-Brüdern ihre alten Planen zum Nulltarif überlassen. Heute existiert ein reger Handel mit dem einstigen Abfallprodukt und ein bisschen weniger Müll fällt auf die Umwelt zurück – FREITAG sei Dank.
Die FREITAG-Story
Vom 2- zum 200-Mann-Betrieb
25 Jahre ist es mittlerweile her, dass die beiden Brüder Markus und Daniel Freitag, ihres Zeichens Grafikdesigner, auf der Suche nach einer praktischen und widerstandsfähigen Tasche waren, in der sie ihre Entwürfe transportieren konnten. Schlussendlich fanden sie selbst die ideale Lösung und schneiderten im WG-Wohnzimmer aus gebrauchten LKW-Planen, Fahrradschläuchen und Autogurten eine Tasche, die nicht nur ihren Ansprüchen gerecht wurde, sondern sich auch bald zum Kultteil in der gesamten Modewelt mauserte. Von Europa verbreitete sich der Hype schnell bis nach Asien. Inzwischen können die Produkte aus recycelten Materialien bei 24 FREITAG-Stores und 400 Verkaufspartnern weltweit erstanden werden. Die Wiener Zweigstelle befindet sich in der Neubaugasse 26 im siebten Hieb. Hinzu kommt noch der Onlineshop und fertig ist das Freitag-Netzwerk, das mittlerweile 450.000 Unikate aus 460 Tonnen LKW-Planen jährlich herstellt. Dazu zählt nicht mehr nur die allseits bekannte Messenger-Bag aus den Anfangszeiten, es gibt insgesamt 40 Taschenmodelle und 40 Accessoires. Hinzu kommen seit 2014 noch Textilien aus dem auf Bastfasern basierenden, hauseigenen, biologisch abbaubaren F-ABRIC-Rohmaterial. Ein Vierteljahrhundert nach der Firmengründung hat sich die Anzahl der Mitarbeiter verhundertfacht, von zwei auf 200. Mehr Infos: freitag.ch
Weiterlesen: FREITAG schenkt sich zum Jubiläum einen Glücklichmacher – hier geht es zur Story!